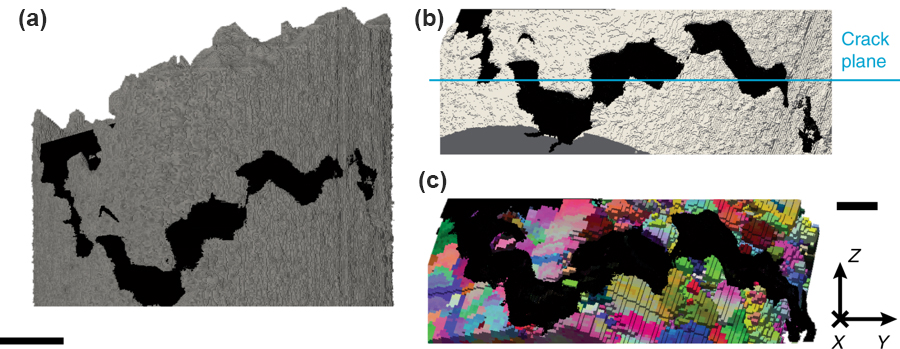
Although crucial to modern life, metal alloys can fail, possibly leading to bridge collapse or other disasters. One cause of failure about which little has been understood is hydrogen embrittlement, which occurs when hydrogen from water propagates a crack. In this work, researchers from academia and U.S. Department of Energy (DOE) national laboratories utilized the U.S. DOE’s Advanced Photon Source (APS) to analyze the micro-structure of a preexisting crack in a nickel superalloy in order to determine the susceptibility of individual grain boundaries to hydrogen embrittlement. By understanding fracture behavior, researchers and industry can better predict metal failure and how to design failure-resistant alloys.
During the 1989 Loma Prieta earthquake, the upper deck of the eastern span of the San Francisco-Oakland Bay Bridge collapsed. Engineers constructed a new earthquake-resistant span, but before the span opened, they discovered that one-third of the steel rods had fractured due to hydrogen embrittlement (HE). While this discovery averted a potential disaster, the opening of the span was delayed by a few years and the fix was extremely costly.
Metal alloys are made of microscopic crystal grains. When hydrogen, typically from water, infiltrates the metal, it propagates cracks along microstructural defects at grain boundaries. This reduces the cohesive strength of the grain boundaries and allows dislocations to nucleate, resulting in sudden fracture. Since the mechanisms of HE are poorly understood, researchers have been unable to predict which metal alloys will fail. At this time, engineers reduce the chance of metal failure by adding additional material, which was the solution to make the eastern span safe. A better understanding of HE has the potential to save time and realize huge economic benefits.
In the past, engineers learned about metal failure by analyzing the separated pieces of a fractured component. But now there are new tools to help solve this old problem. For this paper, the researchers experimented with nickel (Ni)-base superalloy 725. Although engineered for high strength and corrosion resistance, the alloy is very susceptible to HE fractures. Researchers electrically charged a 1 mm cylindrical sample of alloy 725 with H and loaded it to failure in tension. Within the sample they placed the tip of a large, intergranular secondary fracture. Two non-destructive, synchrotron-based techniques revealed the total crystallographic character of individual grain boundaries, including grain orientations: near-field, high-energy diffraction microscopy (HEDM) to image grain shapes and orientations, and x-ray absorption tomography (XRAT) to reveal the interconnections of individual grain boundaries with crack morphology (Fig. 1). Both were done on X-ray Science Division beamline 1-ID-B,C,E at the APS, which is an Office of Science user facility at Argonne National Laboratory.
The researchers in this study, from the Massachusetts Institute of Technology, Johns Hopkins University, Carnegie Mellon University, Lawrence Livermore National Laboratory, Argonne, and Texas A&M University identified ten microscopic structures that contained grain boundaries especially resistant to crack propagation from HE. These grain boundaries deflected a propagating crack to a meandering path, increasing the crack’s surface area and the work necessary for it to grow, making the material less susceptible to fracturing. Nine of these fracture-resistant microscopic structures were “BLIPs,” or grain boundaries with low-index planes, where at least one of the grains had a low Miller index facet. The strongest section of a grain boundary determined the ability of the material to stop or deflect a crack. No cracks were initiated in the sample interior, suggesting that all cracks in the Ni-alloy initiated at free surfaces.
As a result of this work, engineers can use microstructure design techniques to create a more HE-resistant metal alloy. They also can predict the chance of HE failure based on the density and distribution of BLIPs in the microstructures. Although BLIPs are resistant to HE fractures, the researchers did not discover if non-BLIPs preferentially form cracks. In the future, engineers working on bridges will have the tools to design HE-resistant metals. Meanwhile, the microstructure of existing metal components can be imaged to predict their susceptibility to failure. — Dana Desonie
See: John P. Hanson1, Akbar Bagri1,2, Jonathan Lind3,4, Peter Kenesei5, Robert M. Suter3, Silvija Gradečak1, and Michael J. Demkowicz6*, “Crystallographic character of grain boundaries resistant to hydrogen-assisted fracture in Ni-base alloy 725,” Nat. Commun. 9, 3386 (2018). DOI: 10.1038/s41467-018-05549-y
Author affiliations: 1Massachusetts Institute of Technology, 2Johns Hopkins University, 3Carnegie Mellon University, 4Lawrence Livermore National Laboratory, 5Argonne National Laboratory, 6Texas A&M University
Correspondence: *[email protected]
This work was supported by the BP-MIT Materials and Corrosion Center. Access to shared experimental facilities at MIT was provided by the MIT Center for Materials Science Engineering, supported in part by the MRSEC Program of the U.S. National Science Foundation (NSF) under award number DMR-0213282. Work at CMU was supported by U.S. DOE Office of Science-Basic Energy Sciences grant DESC0002001. Computational support for this research was provided by grant TG-DMR130061 from the NSF Extreme Science and Engineering Discovery Environment advanced support program. A.B. acknowledges support from the NSF, Grant No 1150862, for support in HEDM data analysis. J.P.H. acknowledges the DOE Office of Science Graduate Fellowship Program, made possible in part by the American Recovery and Reinvestment Act of 2009, administered by ORISE-ORAU under contract no. DE-AC05-06OR23100. This research used resources of the Advanced Photon Source, a U.S. DOE Office of Science User Facility operated for the DOE Office of Science by Argonne National Laboratory under Contract No. DE-AC02-06CH11357.
Argonne National Laboratory seeks solutions to pressing national problems in science and technology. The nation's first national laboratory, Argonne conducts leading-edge basic and applied scientific research in virtually every scientific discipline. Argonne researchers work closely with researchers from hundreds of companies, universities, and federal, state and municipal agencies to help them solve their specific problems, advance America's scientific leadership and prepare the nation for a better future. With employees from more than 60 nations, Argonne is managed by UChicago Argonne, LLC for the U.S. Department of Energy's Office of Science.
The U.S. Department of Energy's Office of Science is the single largest supporter of basic research in the physical sciences in the United States and is working to address some of the most pressing challenges of our time. For more information, visit the Office of Science website.